PRO (WA): Using Non-Cannabis Items in a Production Run
Creating a Bill of Materials and Production Run Including a Non-Cannabis Item
This article will walk you through the process of creating a Bill of Materials and Production Run to track the use of non-cannabis inventory in Cultivera Pro.
Keep in mind this workflow only pertains to using non-cannabis items in production runs. Non-Cannabis Inventory does not track the Cost of Goods Sold.
The Inventory Management > Production page gives you the ability to create production runs for converting one inventory type into another. Examples include packaging bulk flower into pre-packed units or converting trim, flower, or oil into concentrates, edibles, or other products.
You can now include Non-Cannabis inventory types as inputs for production runs to keep track of any non-cannabis inventory used in the production of your products.
A Bill of Materials is a “recipe” for the product you are producing. It stores the input and output inventory types you’re converting and can be used for multiple production runs or conversions.
Creating A New Non-Cannabis Bill Of Materials
Follow these steps to create a new Bill of Materials (BOM) that includes non-cannabis inventory types.
- Navigate to Production > Bill Of Materials.
- Click the “+ New Bill of Material” button on the top left.
- Enter a name for the conversion that describes what is being processed, and select a type of output product for the conversion process.
- In the second dropdown menu, select the input product type(s), including at least one of "Non-Cannabis" Inventory Type. You can add as many inputs as you need by clicking “+ Add More Input”.It’s a good idea to remove any empty fields that are not in use by clicking the "remove" link.
- Once you have all fields configured, click “+ Create Bill of Materials” and the new Bill of Materials will be accessible from the main Production page and can be used as a template for production runs.
New Non-Cannabis Production Runs
Create a Production Run that includes Non-Cannabis by following the following steps:
- Navigate to Production > Bill Of Materials and click the “+ New Production” button next to the Bill of Materials that you want to use.
- The New Production Run screen is where you’ll enter the specific output product and input product you’re working with.
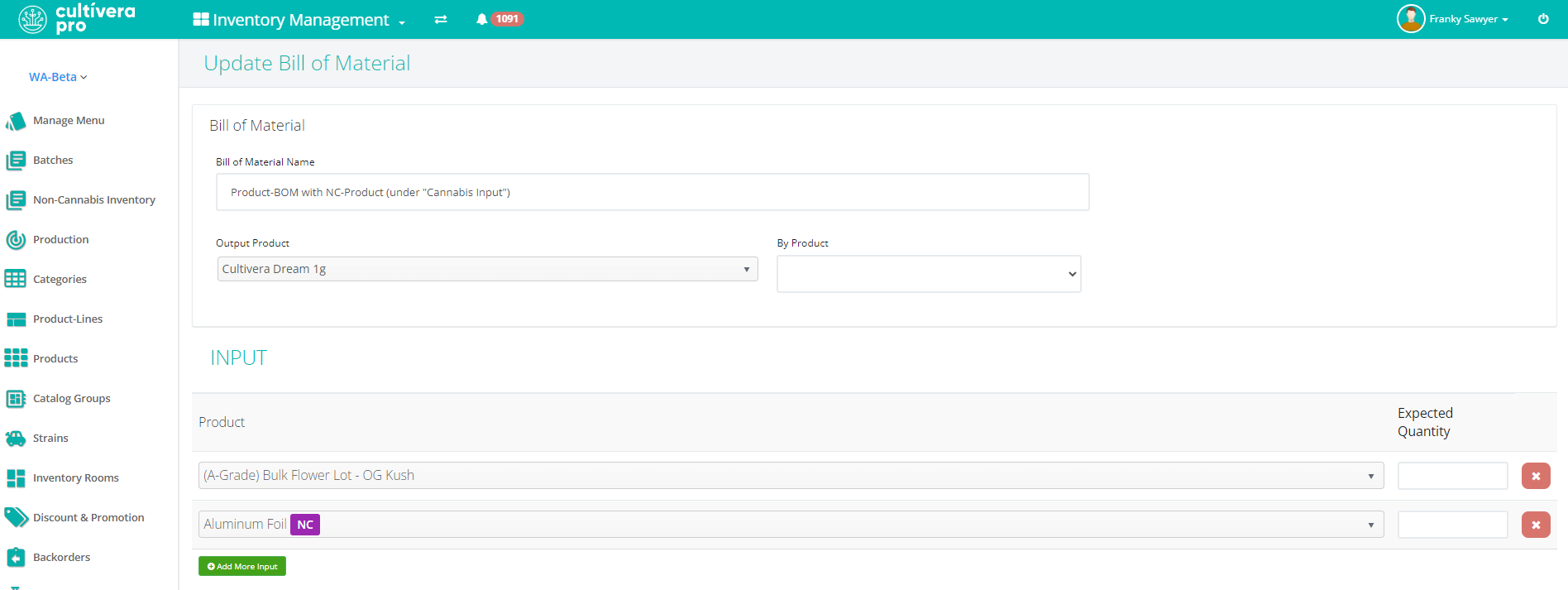
- When you are finished adding the output and input products, click “Create Production Run”.
- A green notification will appear in the upper left corner to confirm that the production run was created and you will be taken to the Production Run screen where you’ll add your allocation and yield for the run.
These entries are typically made after the physical processing or packaging has taken place so you'll already know exactly what amount was allocated and what the final yield was.
- The first data entry field is “Derivative Quantity/Yield”. Enter the yield by inputting either the weight or the number of units you converted, accounting for any waste, as needed.
- Choose whether the new product will require QA testing based on the laws in your area. Typically a product will require testing if it changes physical form, such as converting from trim to concentrate. If you are repackaging something that has already been tested, selecting “No Material Change Requiring additional QA testing” will allow the test results to carry over from the source package, also known as the “QA Parent."
- Using the dropdown menu on the left, select the Room where the inventory will be stored after the conversion is complete. The Planned Production Date is optional, but can be useful if you plan on allocating material to a run you’ll do in the future.
- On the bottom section of the screen, enter your Conversion Input(s), which are the source batches you’re using for the production run. Verify the correct inventory item description is visible and click “Allocate Inventories” to select which batch to use. Enter the number of grams or units you’re using from the original batch then click “Add Selected” to allocate the weight.Tip: If you’re using the entire batch, you can select the full amount of the batch by clicking the green plus sign, then choose “Add Selected”.
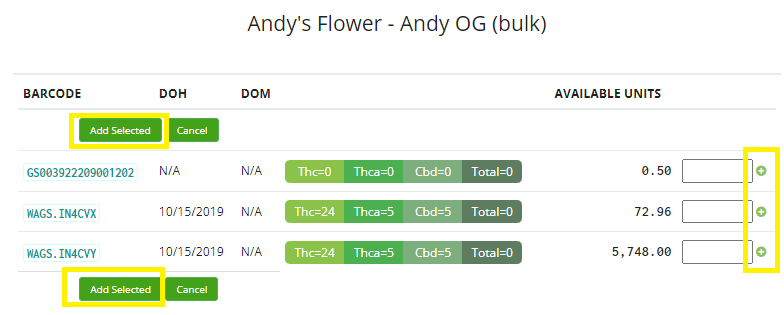
- To automatically make the finished production batch available in inventory, select the "Make new batches available" checkbox, then click “Finalize Production Run” to complete the process.
Often batches aren't made available until after testing has been added, so if you don’t select the checkbox you’ll be able to navigate to Inventory Management > Batches to make the new batch available.
Once the Production Run is complete you’ll see a confirmation screen and the new barcode ID assigned to the new batch will show in the Conversion Summary section.
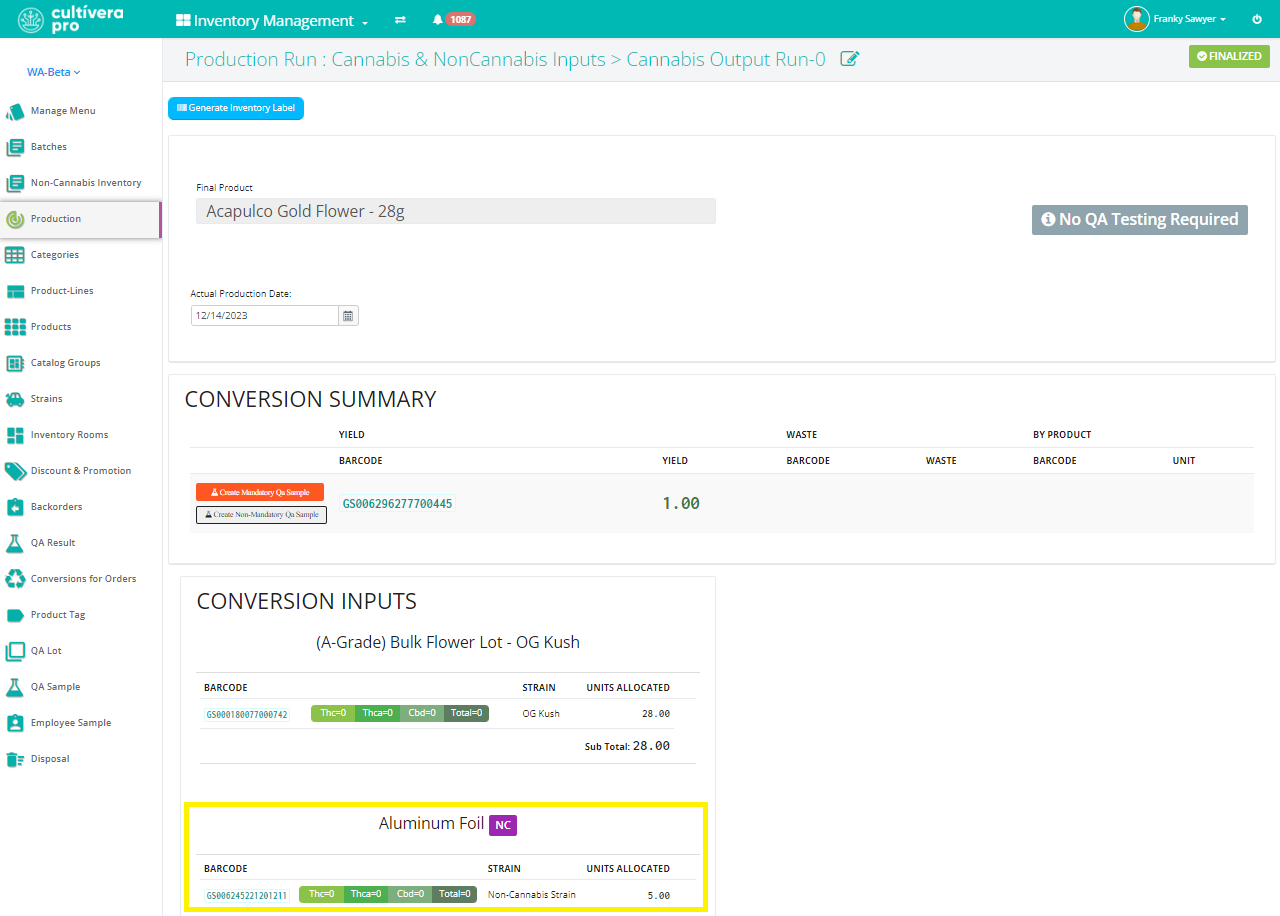
Use the "Generate Inventory Label" button at the upper left of the screen to create an inventory label for the completed batch so it can be tracked in your warehouse.
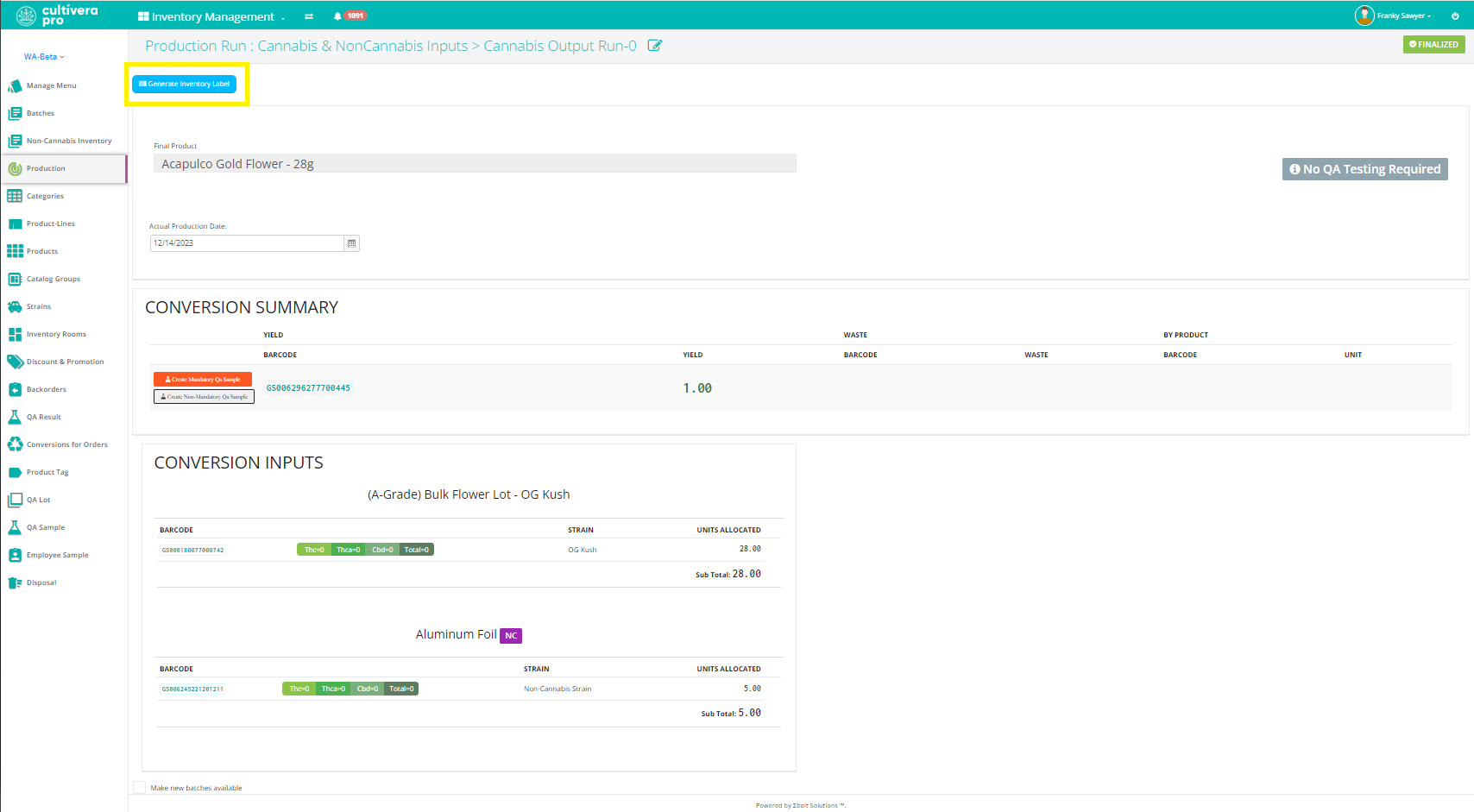
Details about your run can now be found on the “Conversions/Productions” tab at the upper right of the main Productions page. This is where you can generate inventory labels for output products and do “re-runs” of any previous production runs using the green “Re-Run” buttons on the right.

The Batch that you just created can now be found on the Inventory Management > Batches page.

If you have any questions on this or any other workflow in Cultivera PRO, please email support@cultivera.com.